Technical advice & structural design support
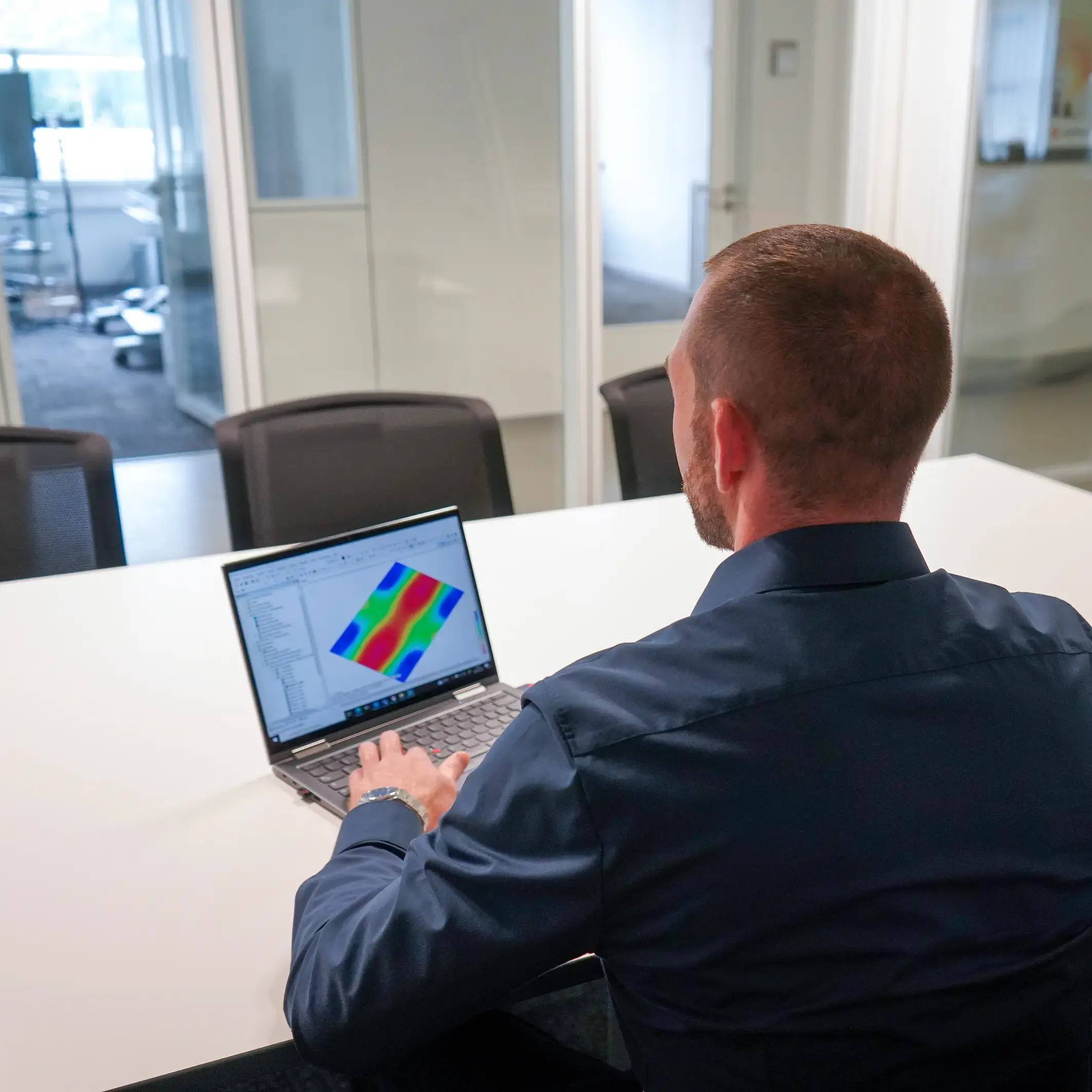
Our structural engineers support you or your engineers in dimensioning of solidian reinforcements. Our experts have more than twelve years experince in carbon reinforcements, carbon concrete and textile-reinforced concrete and are the leading specialists in this field.
In daily planning practice, e.g. in engineering offices, the building material carbon concrete has not yet become established. To change that we are on the mission to help you to learn and spread our knowledge. Therefore, we have created an example for the design of a balcony slab with solidian GRID which our sales team could send you. Feel free to contact us!
We are not doing verifiable structural calculations, but will support you to do your own.
Approvals, certifications & declarations
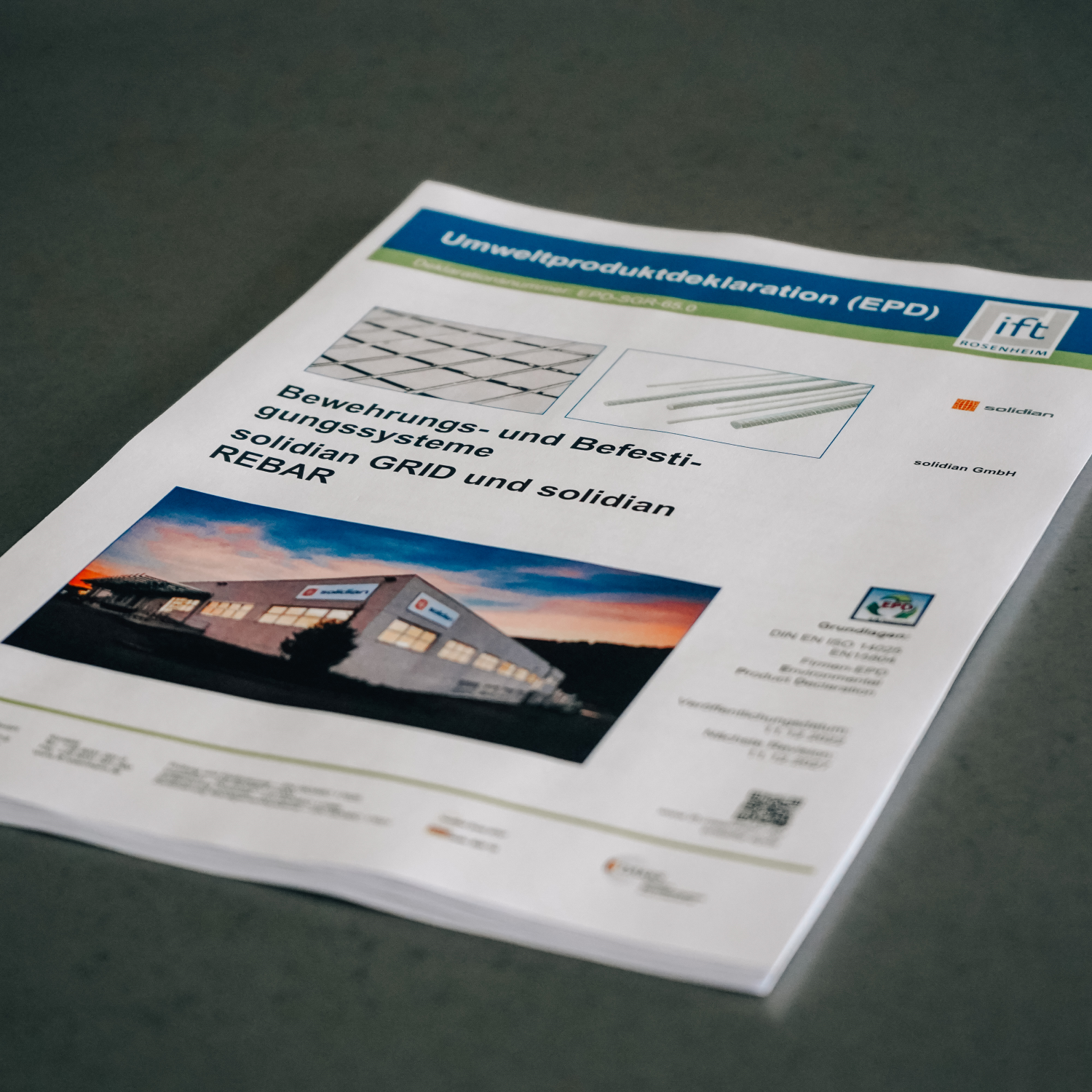
We have approvals, certifications and declarations to ensure smooth work with our products. We are particularly proud to be able to offer a German national technical approval (abZ) and a general construction technique permit (aBG) for the design of our solidian GRID carbon reinforcement. This makes us the first and only manufacturer in Germany to do so. In combination with the DAfStb guideline "Betonbauteile mit nichtmetallischer Bewehrung" (Concrete components with non-metallic reinforcement), this makes it easy to design in accordance with recognized engineering standards.
Furthermore, we have a European Technical Assessment for CRM application (Composite reinforced mortar systems for strengthening concrete and masonry structures) for our reinforcement system solidian ANTISEISMIC with the products ANTISEISMIC Grid, ANTISEISMIC Corner and ANTISEISMIC Connector LCO.
Due to the ecological demands on buildings, we also provide you with an EPD so that the CO2 footprint of your building can be determined.
- National technical approval (abZ) for solidian GRID
- General constrcution technique permit (abG) for solidian GRID
- European Technical Assessment (ETA) for parts of solidian ANTISEISMIC system
- Environmental Product Declaration (EPD) for solidian GRID and solidian REBAR
- DoP declaration
- ISO 9001 certification
- ISO 14001 certification
Tenders, technical data sheets & CAD/BIM details
Great, you are ready with your plannings and want to start into an open competitive bidding? Take a look on our German tender textes you can download here and here.
If you need all our technical data and keyfacts for you planning, you could download all our technical data sheets here.
For the future we will provide CAD/BIM details for our products.
We are here to roll up our sleeves for you: online & on-site
We know that you and your team may be new to carbon reinforced concrete and our reinforcements, so we are happy to help with any questions, whether online or directly on site. We are here for you either on your construction site or at your precast plant.
We are hands-on with help and advice and will show you what needs to be considered when building with our products. We will help you to achieve the best results.
- Advantage
- Application
- Material characteristic
- Test, design & approval
- Economy
- Health, safety & environment
- Handling
- Composite industry
- Can carbon reinforcement be used instead of steel?
- Why should you use carbon reinforcement as opposed to reinforcing steel?
- What are the main advantages of fiber reinforced composites compared to metals?
- Is it possible to reduce the weight of a concrete element with carbon fiber reinforced concrete?
- What positive effects does the use of carbon reinforced concrete have on architecture?
- What is the future of textile and carbon reinforced concrete?
- In which areas can carbon reinforced concrete be used?
- Is it possible to combine steel reinforcements and carbon reinforcements?
- How to produce lightweight concrete elements?
- I want to minimize cracks in my concrete structure. What type of solidian product can I use?
- Can I carry out concrete repairs with your fiber composite reinforcements?
- Can I replace damaged concrete members in structures with carbon reinforcement?
- Can FRP be used to repair reinforced concrete beams and girders in a parking garage when the slab supported by the beams and girders is also a parking lot?
- What steps are required to prepare the existing (damaged) concrete for the use of FRP to reinforce the structure? What about cases where the reinforcing steel is corroded and the concrete has spalled?
- Are coatings based on fiber-reinforced plastics impermeable to water?
- What to consider for reinforcement in concrete furniture?
- What is FRP reinforcement?
- What is carbon reinforced concrete?
- What is the difference between steel reinforced and carbon reinforced concrete?
- Is carbon fiber stronger than steel?
- What is the strength of carbon reinforcement?
- How durable is carbon reinforced concrete?
- Is FRP reinforcement UV-resistant?
- Is carbon reinforced concrete fire resistant?
- Does carbon fiber conduct electricity?
- How is a carbon textile made?
- How are carbon fibers obtained?
- What method exists for producing carbon reinforced concrete?
- What materials are solidian FRP reinforcement products made of?
- Do approvals exist for solidian FRP products?
- Which standard can I use for the design of components with reinforcement made of fiber-reinforced composites?
- Is there a design software from solidian for FRP products?
- Do you also provide static calculations for the constructions with FRP reinforcement?
- Which tests on the products are carried out by solidian as standard?
- How expensive is carbon reinforced concrete compared to steel reinforced concrete?
- Are the solidian FRP reinforcement materials harmful to health?
- How environmentally friendly are FRP composite materials?
- Is it possible that solidian supplies LCA data of their FRP reinforcements or the products reinforced with these?
- Do solidian FRP reinforcements have a lower CO2-footprint than steel reinforcements?
- Do concrete applications reinforced with solidian FRP products have a lower CO2-footprint than steel-reinforced concrete products?
- What are the resource and material savings when using carbon-reinforced concrete?
- How do I dispose of solidian's FRP reinforcements waste?
- Is it possible to recycle carbon reinforced concrete?
- What do I need to consider when transporting and storing FRP reinforcement?
- Is local bending of FRP reinforcement possible?
- How can FRP reinforcing mats or rebars be connected to each other?
- Do I need special spacers when using FRP reinforcement?
- Does the FRP reinforcement show on the concrete surface (ghost reinforcement)?
- What is the sieving effect when concreting a concrete element with FRP reinforcement?
- How can the floating of the FRP reinforcement be prevented?
- What do I have to consider when I want to install add-on parts on any FRP reinforcement?
- Can FRP reinforcement be welded?
- Is walking and driving on the FRP reinforcement allowed?
- How can FRP reinforcement best be shortened or cut into shape?
- Can drilling, (water jet) cutting and milling be used on concrete components with reinforcement made of fiber reinforced composites?
- Will you also make new products that are not in your standard portfolio?
- Is Kelteks ISO 9001:2015 certified?
- What is a composite?
- Is Kelteks ISO 14001:2015 certified?
- What are the primary advantages of composite materials?
- What is the purpose of reinforcement in composites?
- Where should I use glass fiber and where to use carbon fiber?
- Where are composites used?
- What are the three general factors that determine the properties of a composite material?
- up to several times higher characteristic tensile strength for carbon reinforcements
- non-corrosive
- low weight
- very high alkali resistance
- insensitive to a variety of aggressive media
- long service life
- electrically conductive (special product variants of carbon reinforcement)
- easy to drill through (only glass fiber reinforcement)
- electrically non-conductive (only glass fiber reinforcement)
- non-magnetizable (only glass fibre reinforcement)
- thermally insulating (only glass fiber reinforcement)
- resource-saving due to the possibility of building thinner and thus saving cement, water and aggregates and finally
- reduction of CO2 emissions by saving material and energy (e.g. lower transportation costs for prefabricated parts)
- the material: steel vs. carbon composite as a reinforcement in the concrete
- the tensile strength of the reinforcement: carbon reinforcement is stronger than steel reinforcement, which means that the component can be built thinner or can be exposed to higher loads (provided that the limitation of cracks is not the primary concern).
- solidian GRID carbon reinforcement mesh for the reinforcement of concrete components: abZ/aBG Z-1.6-308 (Germany)
- CRM reinforcement system solidian ANTISEISMIC for structural reinforcement of concrete and masonry structures: ETA 23/0383 (Europe)
- Carbon reinforcement grid solidian GRID for reinforcement of concrete components: ETA (Europe)
- Carbon reinforcement mesh solidian ANTICRACK for reinforcement of concrete components: abZ/aBG (Germany)
- Glass fiber reinforcement bars for reinforcement of concrete components: abZ/aBZ (Germany)
- Concrete sandwich wall system solidian SANDWICH WALL SYSTEM: abZ/aBZ (Germany)
- Screed reinforcement solidian PRIMAFLOOR: ETA (Europe)
- solidian sandwich wall: abZ Z-71.3-39,
- solidian façade panel: abZ Z-71.3-41 and
- solidian small buildings, room cells (prefabricated garage): abZ/aBG Z-71.3-40
- Glass fiber reinforced composites (GFRP)
- Basaltic fiber-reinforced composites (BFRP)
- Aramid fiber-reinforced composites (AFRP)
- Carbon fiber reinforced composites (CFRP)
- The primary advantage of composites is the ability to specifically design the properties of a material by combining different material components that are bringing in their special properties. In this way, composites can be specifically optimized to create e.g. a very light material in combination with very high strength. This combination is one of the aims to create and use fiber-reinforced plastics (FRP). These are lightweight and very strong at the same time.
- Another example is the class of composite materials made of concrete matrix and fiber reinforced plastic (FRP) reinforcement for the concrete. Here the material follows the aim to combine the high compressive strength of concrete with the high tensile strength of the FRP reinforcement. The FRP reinforcement additionally brings in its high media resistance avoiding rusting of buildings and increasing lifetime.
- Both examples have furthermore in common that the reinforcements (fibers respectively FRP) can be specifically integrated only in those areas and directions where you need it. This enables optimization of weight and strength and furthermore reduction of resources.
frequently asked questions
Yes, reinforcement made of carbon fiber reinforced polymers even has higher tensile strength, making them superior to steel in terms of force absorption. A major advantage is that carbon reinforcement does not corrode and thus the concrete cover can be significantly reduced.
Carbon reinforcement can be used as the corrosion-free pedant to steel reinforcement. There are no restrictions in terms of applications.
If special requirements, such as freedom from magnetism, no thermal conductivity or no electrical conductivity, require the use of reinforcement with these properties, glass fiber reinforcement is the best choice. Glass fiber reinforcement also does not corrode.
Fiber reinforced polymers have several advantages over metals. In particular, reinforcements made of fiber reinforced composite materials are convincing in the following points due to their material parameters.
These properties open up essential benefits:
Simply put, yes! In connection with the use of fiber composite reinforcement, it is possible to reduce the required concrete cover to a minimum. Fiber reinforced polymer (FRP) reinforcement does not corrode. Therefore, no concrete cover is necessary due to durability requirements. Only the bond between the reinforcement and the concrete must be ensured.
For example, the facing shell of a sandwich façade can be reduced by half its thickness, which means a weight saving of approx. 50%.
The use of carbon reinforced concrete (or carbon concrete for short) allows thinner, filigree components and building structures such as façade panels and shells to be realized, as the concrete cover can be reduced to the minimum required for force transmission, in contrast to reinforced concrete. Steel needs concrete as corrosion protection - fiber reinforced plastics do not need protection because they do not rust! In addition, the use of textile fabrics as reinforcement allows almost any shape to be produced as concrete components. Twisted components, expressionist façades or very simple concrete furniture are just a few examples.
Regardless of whether there is glass fiber or carbon fiber reinforcement in the concrete, all fiber reinforced composites have one thing in common - they have a decisive advantage over reinforcing steel: they do not corrode! And with this positive property, many advantages can be generated when building with carbon concrete compared to conventional construction with reinforced concrete. Today, fiber reinforced composites are not yet as widely used as reinforcing steel in the construction industry. However, the topic is gaining momentum and they will therefore be used more and more frequently in the future, especially as the legal basis for the use of the material and the dimensioning of the components is created.
Carbon reinforced concrete (in short: carbon concrete) can generally find application in any structural component or building structure. However, today the applications for carbon reinforcements tend to focus on those found in outdoor areas or in direct contact with aggressive media. Examples include Hydraulic structures, maritime structures, wastewater treatment plants, agricultural structures, concrete facades (especially rainscreen cladding panels, sandwich walls), bridges (especially bridge caps and bridge decks), parking decks, gas station areas, and surfaces that place special demands on the cracking behavior of concrete. Glass fiber reinforcement can also be used when special requirements are placed on the structural component. The special material properties of glass fiber reinforcement, such as thermal insulation, non-magnetic and non-electrically conductive, make it economical to use in areas of high-voltage installations and electromagnetic fields, where the use of steel as reinforcement must be ruled out.
Yes, in general it is possible to combine steel and carbon fiber reinforcement unless it is excluded by national regulations. However, you must ensure that there is no contact between the steel and the carbon fibers.
To avoid so-called "galvanic corrosion", it is necessary that the carbon fiber reinforcement is insulated, e.g. with a plastic spacer. Please note that the insulation area does not negatively affect the bond between the reinforcement and the concrete.
The same applies to reinforcement made of glass fiber composites, but no measures are necessary here to prevent galvanic corrosion.
There are several ways to realize lightweight construction with concrete. However, in conjunction with fiber composite reinforcement, the first option is to reduce the concrete cover required for the reinforcing steel to a minimum. The fiber composite reinforcement does not corrode and therefore does not require a concrete cover that meets the standards for reinforced concrete components. The only thing that needs to be ensured is a cover to guarantee the bond.
For example, the thickness of a shell can be reduced by half. In addition to the lower component weight compared to reinforced concrete, the filigree appearance is a key aspect.
A second possibility is to exploit the performance of the carbon reinforcement, which has a several times higher tensile strength, in order to design thinner construction elements.
In general, only epoxy resin-impregnated fiber composite reinforcements are able to significantly reduce the crack widths in concrete components. Due to their high stiffness, carbon reinforcements with epoxy impregnation are the most efficient material for these technical requirements.
A special grid for effectively minimizing crack widths is called solidian ANTICRACK. It is a solidian GRID carbon reinforcement with a specially sanded surface.
In general, concrete repairs can be carried out with reinforcements made of fiber-reinforced plastics as a replacement for reinforcing steel. Please observe the relevant national standards for carrying out proper concrete repairs.
Simply put, all existing spalling in the concrete must be removed and the substrate prepared with suitable materials. Then the fiber composite reinforcement is installed using standard concrete or polymer-modified concrete/mortar.
The design of the FRP reinforcement can be based on restoring the original (or required) strength of the structural members. This can be done by measuring the residual cross-sectional area of the steel bars after cleaning to remove rust or corrosion residues. If the component has a high chloride content, an anti-corrosion system may be required to protect the existing steel bars and prevent further deterioration. This should be done before the FRP reinforcement is installed.
Yes, if the existing components have suffered damage due to water ingress, chloride ingress or similar (corrosion of steel bars and spalling of concrete), FRP can be used to restore the capacity of the damaged components. However, proper concrete repair measures must be carried out before the FRP is applied.
All existing cracked and spalled concretes must be removed and the substrate repaired using appropriate concrete repair materials. Then the surface is prepared and FRP reinforcement can be installed. The design of the FRP reinforcement can be based on restoring the original (or required) strength of the structural components. This can be done by measuring the residual cross-sectional area of the steel bars after cleaning to remove rust or corrosion by products. If the member contains a high level of chloride the corrosion protection system may be required to protect the existing steel bars and prevent further deterioration. This should be done prior to FRP reinforcement.
If the surface of the component is completely covered with FRP, no water (or oxygen) can penetrate.
Glass fiber reinforcement is sufficient for concrete worktops in kitchens that are laid every 60 cm during installation and have a panel thickness of 3-4 cm. A fine-mesh reinforcement grid made of glass fiber composite material, e.g. solidian GRID, is recommended here. For higher transport loads or recesses, a small-mesh carbon reinforcement, e.g. solidian GRID, is recommended. For longer, self-supporting components, such as table tops or benches, solidian GRID carbon reinforcement is recommended. For example, a solidian GRID Q95-CCE-38 is used for a bench with a length of 2 m and a panel thickness of 3 cm. This is also recommended for table tops.
If the concrete is to be poured using the lamination process, a fine-mesh mat can also be used. As a general rule, the finer the reinforcement, the better the formability and drapability.
For load-bearing concrete parts, solidian recommends concretes of grade C50/60 or higher. The grain size depends on the thickness of the component. Concrete means a minimum grain size of 8 mm, for components less than 3 cm thick, a fine concrete (mortar) is recommended.
FRP reinforcement is an abbreviation for Fiber Reinforced Polymer reinforcement. FRP reinforcement consists of high strength/high stiffness fibers combined with a suitable resin to form a rod or grid. The most commonly used fiber today is glass, combined with a vinyl ester, SBR, or epoxy resin, although carbon fibers with epoxy resins are more and more available for load-bearing applications.
Carbon-reinforced concrete (or short: carbon concrete) is concrete for building structures reinforced with carbon reinforcement (meshes or rebars). It’s a sustainable alternative to conventional concrete structures reinforced with steel (meshes or rebars).
Main differences are:
If by “stronger” you mean force transmission, then yes, as long as it is a tensile force.
Carbon reinforcements are approx. 3-5 times more powerful than conventional reinforcing steel under tensile loads and in relation to design loads.
If you compare the strength characteristics of our products with those of other manufacturers, it is important that the comparison is made under the same boundary conditions!
Comparisons in tensile strength can only be made in relation to:
1. the pure fiber cross-section (area of the statically effective pure fibers without impregnating agent or resin matrix) or
2. the nominal cross-section. The nominal cross-section describes the composite cross-sectional area (fibers and impregnating agent), which is used as a reference value for determining strength and stiffness-related reinforcement properties. This applies to bars and grids.
In our technical product data sheets, we state strength values in relation to the fibers used and/or also in relation to the composite cross-section.
Furthermore, our products are made for use in the construction industry - therefore, in addition to the information on mean values, characteristic values are also shown, which represent the relevant value for the short-term tensile strength. The characteristic value should therefore indicate the strength of the material that is exceeded in 95% of all components (5% quantile).
Last but not least, long-term effects on the tensile strength of the non-metallic reinforcement must be taken into account. Therefore, the characteristic short-term tensile strengths must be reduced by a factor depending on the material in order to take into account the effects of durability.
For specific values for our products, please refer to the respective technical product data sheets.
Carbon-reinforced concrete – or carbon concrete for short – is more durable than conventional reinforced concrete due to the material behavior of the reinforcement. Normal steel (with the exception of high-quality stainless steel) corrodes if the concrete structure is not built of high quality, is damaged, or exposed to aggressive media (e.g. road salt, saline water, sewage, slurry, fuels, etc.). Corrosion of steel means damage to the steel (reduction of material in cross-section and thus loss of absorbable tensile force), to the concrete (spalling of the concrete cover) until finally, the entire structure may fail. The reinforcement made of fiber-reinforced polymers inserted in the carbon concrete cannot corrode and thus cannot cause any damage to the structure due to rust. This means that carbon concrete structures can have a much longer service life (more than 100 years) than steel reinforced concrete structures.
No, fibre-reinforced composites are generally not UV-resistant unless additives are added to stabilize the polymer structure against UV radiation.
Our reinforcements are usually installed in concrete and do not require high UV stability. They must therefore be protected from UV radiation and moisture until concreting.
Compared to steel, fiber-reinforced plastics are not fire-resistant in general. However, since they are always encased in concrete, fire resistance of the overall component can also be achieved. The thickness of the concrete cover is decisive.
In general, carbon fibers are electrically conductive. The conductivity can be reduced or eliminated if the fibers are embedded in a resin matrix, as is the case with FRP reinforcements. Since defects in the resin matrix cannot be eliminated when using non-metallic reinforcement, suitable measures must always be taken to eliminate the electrical conductivity. Alternatively, glass fiber composites can be used.
Conductive carbon grids are used, for example, as a substitute for titanium anodes in the field of cathodic corrosion protection. Further information can be found on our homepage under solidian eGRID.
Carbon fiber has a diameter of about 5-8 micrometers. Usually, 1.000 to 24.000 individual fibers (filaments) are combined into a bundle (roving), which is wound onto spools. Further processing takes place, for example, on weaving machines or warps knitting machines to form textile structures.
Carbon fibers are industrially produced fibers made from carbon-containing starting materials that are converted into graphite-like carbon by pyrolysis. A distinction is made between isotropic and anisotropic types: isotropic fibers have only low strengths and less technical significance, while anisotropic fibers exhibit high strengths and stiffnesses with low elongation at break.
Carbon concrete is the composition of carbon reinforcement and concrete – similar to steel-reinforced concrete, where the steel and concrete act together.
While the fiber material consists of carbon, glass or basalt fibers, the impregnating material in turn consists of a resin. solidian preferably uses epoxy resin (EP), styrene-butadiene rubber (SBR) or acrylate dispersions (AC or Y).
In most countries around the world, national building regulations require building authority approval in order to install construction products.
We currently have general building authority approvals of a national or European nature for the following products:
Applications have already been submitted or are in the approval process for other products:
Approvals already granted
have expired and are therefore no longer valid.
Due to the new nature of the material, there are currently only a few valid national standards for the design of components, e.g. in the USA, Canada, Italy and Japan.
For Germany, there is currently a guideline from the German Committee for Reinforced Concrete (DAfStb) "Concrete components with non-metallic reinforcement" for the design of reinforcements made of carbon and glass fiber composite plastics.
If no standards for the design of our products can be used in your country, a calculation can be carried out using the existing principles. External research institutes have examined and confirmed these principles intensively and in detail.
A similar situation arises with the use of our construction products - there are only a few valid national product standards for the use of fiber-reinforced composites as reinforcement. If no product standards exist, these must be regulated by national regulations. In Germany, for example, the use of the product is regulated by general building authority approvals (abZ). A comparable European regulation then provides for a European Technical Assessment (ETA).
We use an internal tool to carry out a static calculation for customer inquiries based on the German guidelines of the German Committee for Reinforced Concrete (DAfStb) "Concrete components with non-metallic reinforcement".
Are you interested in this tool? Then get in touch with us!
Our civil engineers will answer you for sure a lot of your questions concerning dimensions and calculations. We are in contact with excellent offices for structural analysis and will support you in finding the perfect partner.
For all products with a national or European technical approval, we carry out internal and external monitoring tests on the product. External monitoring in particular provides an independent assessment of our products and ensures the performance and quality offered.
For products without building authority approvals, visual and tensile tests are carried out as standard. If you require additional tests on these products, please contact us before ordering. We will be happy to advise you.
As fiber reinforced composite materials such as carbon reinforcement are more expensive in direct comparison to steel reinforcement, the construction of concrete structures incurs higher acquisition costs (investment costs), but these are amortized over the service life of a concrete structure or building. Repair costs are minimized - in addition, there are also construction situations that lead to a gain in usable building space that can be profitably rented or sold.
Since the fibers we use (carbon and glass fibers) and the fiber composites we manufacture, such as our solidian reinforcements, are not harmful to health after the resin (especially the epoxy resin) has hardened, solidian reinforcement products can be used without hesitation.
As with all work with materials and tools, please ensure that you wear suitable work clothing and observe appropriate protective measures.
The work in the “Environmental compatibility” project group of the C³ focused on characterization tests on ready-mixed concrete, cement/binder, fillers and carbon fibres as well as on leaching tests according to the European long-term leaching test DSLT (DIN CEN/TS 16637-2:2014) on unreinforced and reinforced fine concrete samples.
The leaching tests of the tested carbon fibers have shown that they release practically no polycyclic aromatic hydrocarbons into the leaching water. Furthermore, it was found that there was no significant difference in the leaching behavior of the unreinforced and reinforced fine concretes for the individual parameters. The results available to date indicate that the material carbon reinforced concrete can be classified as environmentally compatible and therefore no further environmental tests are required.
Since 2019, solidian has been looking at the life cycle analysis of our own products and the customer components manufactured from them in order to determine our impact on sustainability. Part of this work is to determine the necessary material and process data of e.g. production processes, logistical processes and raw materials sourced from external partners such as suppliers.
As solidian itself does not prepare life cycle analyses for components, we can still contribute with material parameters. We have had an environmental product declaration (EPD) drawn up for the first products so that the ecological footprint of our products can be presented transparently.
In terms of GWP per kg, fiber-reinforced plastics such as our carbon reinforcement are certainly worse than conventional reinforcing steel. But simply comparing material parameters is not enough! A direct comparison of materials is only half the truth, because the entire service life of the concrete component made from them must be taken into account.
Reinforcing steel usually has a lower CO2 equivalent than non-metallic reinforcement. However, the ratio depends on the fiber material (carbon or glass), the type of reinforcement (mesh or reinforcing steel) and the type of reinforcing steel (regional energy mix of production, regional recycling rate). This is one of the reasons why one should not only consider the pure CO2 equivalent of the reinforcement, but also evaluate the entire life cycle of a building component or structure.
The use of non-metallic reinforcements helps to reduce massive metallic reinforcements, concrete and thus component weight and material usage. It also extends the service life of concrete components, because where nothing corrodes, nothing can be destroyed and nothing needs to be repaired. All of this - and other aspects - results in a reduction in the CO2 footprint of the entire concrete component or structure. In most cases, this leads to a positive result of the life cycle analysis for non-metallic reinforcements, regardless of regional aspects.
The assessment of the carbon footprint (Global Warming Potential = GWP) or other comparisons to evaluate the sustainability of a product should be carried out in the form of a life cycle analysis (LCA) of the end product over its entire life cycle. This includes all raw materials and energy used to manufacture the part, the entire life of the part, including maintenance and other measures required to keep the part fit for use, the disassembly phase and recycling. solidian analyzes such life cycles with partners. Our results show that the potential to reduce raw materials (up to 50%) and GWP (up to 30%) varies depending on the reinforced part. The main advantages of non-metallic solidian reinforcements are the reduction of the concrete thickness of the component and the resulting use of less concrete and cement, a material that has a high carbon footprint. In addition, the use of non-metallic solidian reinforcement can avoid the need for surface coatings of the concrete parts, as a much finer crack distribution can be achieved than when using steel reinforcement. In a project for a pedestrian bridge, both advantages - reduction in component thickness and no need for surface coating - were utilized, as the above figures show.
In general, the amount of material and therefore resources saved always depends on the component or building structure.
With solidian reinforcement, bridges and façade elements have been constructed in which almost 50% of the material could be saved. And by that we primarily mean concrete! This in turn reduces the use of cement and our natural and scarce resources such as water and sand.
Simply said: Close the material cycle and give offcuts or demolition material to a recycling company that specializes in fibre-reinforced plastics! Carbon fibers in particular are far too expensive to simply throw them away.
Carbon fiber recycling material can be reused in the following applications, for example: As additives for PVC/compound applications, as use of short fibers in non-woven textiles (e.g. for vehicle construction) or for the production of new recycled yarns with similar properties to those made from new fibers.
The demand for recycling currently still massively exceeds recycling capacities. Nevertheless, we have set the task of finding a sustainable solution. We have succeeded in doing so, so that we can provide you with a partner who can also feed your recycled material into new material cycles and not just dispose of it.
Yes, the separation of carbon concrete into the components concrete and carbon reinforcement has already been tested and carried out without any problems. Existing and independently tested processes have been used for this (see C3 - Carbon Concrete Composites e.V.: https://carbon-concrete.org/carbonbeton/recycling/).
The separated concrete can be recycled like normal concrete. The resulting carbon fiber recycling material can be reused in the following applications, for example: As additives for PVC/compound applications, as use of short fibers in non-woven textiles (e.g. for vehicle construction) or for the production of new recycled yarns with similar properties to those made from new fibers.
The demand for recycling currently still massively exceeds recycling capacities. Nevertheless, we have set ourselves the task of finding a sustainable solution. We have succeeded in doing so, so that we can provide you with a partner who can also feed your recycled material into new material cycles and not just dispose of it.
As reinforcements made of fiber composite materials are lighter and more flexible than conventional reinforcing steel, they tend to bend more during transport. Suitable lifting gear must therefore be used, especially when lifting with a crane. Reinforcement grids can be transported either as individual meshes or rolled up. The same applies to reinforcing bars - bars as loose bundles or as coils (depending on the bar diameter).
Reinforcements made of fiber composite materials from solidian GmbH must not be damaged during transport, storage, processing and installation and must not be exposed to temperatures higher than 80°C. They must be kept dry and protected from corrosion. They must be stored dry, protected from the weather and without touching the ground. They must be protected from UV radiation and moisture until concreting and must be free from bond-reducing impurities (e.g. grease, soil, loose concrete residue).
Due to the transverse pressure sensitivity of the composite material, mechanical effects must generally be avoided. Damaged fiber bundles (resin flaking, brittle areas, etc.) should not be installed, as the specified load-bearing capacity cannot be guaranteed.
The reinforcement can be formed into many shapes in the factory by us, but post-forming of edges, stirrups, etc. is not possible on the construction site or in the precast plant.
However, it is possible to extend meshes and bars with a defined bending radius (e.g. in round walls).
In the case of FRP reinforcement meshes and rebars, a temporary connection can be made during concreting using commercially available cable ties. Metallic binders are not recommended or are to be excluded when using carbon reinforcement.
Generally not - all commercially available plastic spacers can be used.
For exposed concrete surfaces in particular, solidian recommends its specially developed solidian SPACER spacers for the solidian GRID mesh reinforcement.
This can occur in a similar way to reinforcing steel reinforcement - partly due to the so-called sieving effect of the meshes when concreting the component, partly due to the fines in the concrete. This can be avoided by changing the concreting sequence (installation in layers) or by changing the concrete mix (maximum grain size and limestone powder). Furthermore, this can be avoided by using spacers that ensure a minimum distance between the formwork and the reinforcement For detailed support, please contact our specialist staff.
The effect can occur during the concreting process with a too large grain size or too fine mesh reinforcement. This effect can be prevented by the lamination process (multi-layer application) during concreting. If multi-layer reinforcement is used, a minimum 38 mm mesh size and fine concrete with a maximum grain size of 8 mm are recommended.
Our reinforcement is lighter than conventional steel reinforcement. Therefore, some self-compacting concretes may float, but this can be avoided by adjusting the concrete formula or by using a suitable spacer or fixing system. For this purpose, we offer spacers, a fixing system, or can recommend a concrete recipe.
The installation of add-on parts by tying them together (wire, cable ties, etc.) is possible at any time. Please note the further measures to avoid contact corrosion of carbon fiber reinforcements in connection with steel reinforcements. The direct installation of add-on parts to FRP reinforcement by welding is not possible! The installation of add-on parts by welding near the FRP reinforcement should only be done after prior consultation with us or the engineering office. In general: excessive heat influence on the fiber plastic reinforcement should be avoided by e.g. welding, as this influence can negatively affect the material structure and thus the load-bearing capacity of the reinforcement.
Welding and soldering of fiber-reinforced polymers is not possible. In general: excessive heat influence on the FRP should be avoided by e.g. welding, as this influence can negatively affect the material structure and thus the load-bearing capacity of the reinforcement.
In general yes, but you need to consider the following for our solidian grid reinforcement:
WALKING – When entering the reinforcement, you have to ensure that the work is only carried out by trained personnel. For this purpose, we offer comprehensive support in terms of personnel instruction and on-site training by its application technology. It is essential to avoid stepping on cavities where reinforcement is laid out in order to avoid damage and breakage of the laid-out fiber material.
DRIVING – Any kind of driving with vehicles or equipment is prohibited. This will result in damage to the fiber material. The intended performance of the reinforcement can therefore not be achieved.
Important preliminary information!
In general, all FRP should be cut dust-free. For all work with cutting equipment, the appropriate protective measures must be observed, such as wearing cut-resistant gloves, safety goggles, ear protection if necessary, and a dust mask. For our solidian products and other carbon fiber-based products, no electrical devices that generate dust (e.g. cut-off grinders) may be used.
For our mesh reinforcement solidian GRID and solidian ANTICRACK, independent of glass or carbon fiber, sheet shears (battery or compressed air operation) are optimally suited. Other products based on a flat textile grid structure can also be processed with tin snips. Our bar reinforcement solidian REBAR or the mesh reinforcement solidian REMAT based on glass fiber can be shortened (manually) with a simple metal saw. We recommend processing our bar reinforcement based on carbon fibers with compressed air tin snips. The same procedure applies to all solidian products with an accumulated textile structure.
Yes, just as with metal-reinforced concrete components, conventional processing methods can be used. A great example comes from tunnel construction, where tunnelling machines can drill directly through the soft eyes without stopping the drive. The glass fiber reinforcement enables direct driving in the concrete component, which would not be possible with conventional reinforcing steel.
The appropriate health and safety measures must be observed for all methods.
Yes of course. We are constantly upgrading our product portfolio together with our partners. Feel free to contact us with your ideas.
Yes, we are. You can find our certificate here: Certificate Kelteks ISO 9001:2015
A composite is a material that consists of two or more material components that are combined with each other. A composite has different properties compared to the properties of each single material component, which is the reason why composites are used. Composite materials can be differed according to the geometry of their components. There are the following types:
– Particle composites => at least one component is particle-like, e.g. polymer concrete
– Fiber-reinforced composites => at least one component is fiber-like, e.g. fiber reinforced plastic
– Laminate composite => the components are layers, e.g. aluminum Dibond plates
– Penetration composites => one component has a porous like structure filled up by at least a second component, e.g. ceramics like silicon infiltrated silicon carbide
Each component of a composite of the different kinds can be made of different materials.
Keltkes products are mainly found in the group of fiber-reinforced composites using, glass, basaltic, aramid, or carbon fibers as reinforcement and polymer matrix. The fibers are carrying the loads, whereas the matrix has the function to transfer the loads to the fibers and fixing the geometry of a part. These composites are called fiber-reinforced plastics (FRP) or specifically:
Yes, we are. You can find our certificate here: Kelteks Certificate ISO 14001:2015
The reinforcement in fiber-reinforced plastic composites has to carry the loads of the application that is produced. The plastic (polymer) matrix has to hold the fibers in place and spread forces into the fibers of the reinforcement.
For reinforcement of concrete: If you need non-conductivity or thermal isolation properties you clearly need to use glass fibers. If you need the highest tensile strengths or stiffnesses with small diameters or if you look for lifetimes much more than 100 years you need to use carbon fibers. For all other cases, you can look for the best price-performance ratio that can vary depending on the reinforcement type or critical load case of your application. Composites in General: Carbon fibers should be used where you have very high demands regarding lightweight due to the higher strength, higher stiffness, and lower weight of carbon fibers. Glass fibers offer a good price-performance balance.
Composites are used in nearly all application fields of today’s world, especially where lightweight and saving resources is key aspect. Examples are the construction industry, automotive industry, aerospace industry, boat building, tubes and containers, sports articles, and consumer products.
There is a number of properties determining the material behavior of composite materials. The main categories are Lightweight, high mechanical properties, and media resistance.